A new generation of thermoset materials for your technical parts
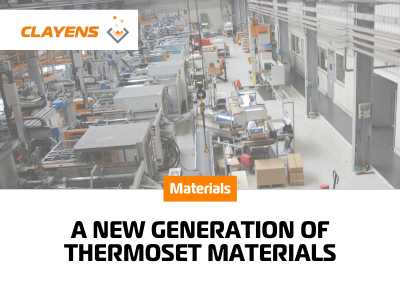
As a specialist subcontractor, particularly in thermoset materials, CLAYENS supports its clients' projects with a new generation of thermoset composites featuring unique properties.
As a reminder, thermosets (or thermosetting plastics) are materials that harden progressively under the effect of heat until they reach an irreversible solid state. Once cured, they cannot be recycled.
Before diving into the details of this new generation, let’s revisit the characteristics of thermoset materials.
What are the advantages of thermoset composites for technical parts?
These materials offer numerous advantages for a wide range of applications, particularly in the field of electrical components. Key benefits include:
-
Reduced material cost,
-
Excellent heat resistance, ensuring dimensional stability even after exposure to thermal shock
-
Outstanding fire resistance, especially in the event of a short circuit, without relying on toxic or hazardous substances
-
High durability: over 20 years
-
Ability to mold thick wall sections without the risk of sink marks
These features make thermoset composites a material of choice for many applications, in our case, structural and/or safety components in electrical equipment. This type of composite meets the sector’s strict standards for safety, longevity, and performance.
Thermoset composites: limitations to consider
Traditional thermosets, such as SMC or BMC, do have some limitations:
-
Relatively long production cycles, typically lasting several minutes. This is mainly due to the polymerization process required to transform the material. In comparison, thermoplastics allow for much shorter cycles, often under a minute.
-
Mandatory deburring, along with the presence of sprues*, leading to material loss and the generation of non-recoverable waste.
These constraints are currently driving the development of innovative processes aimed at maintaining the advantages of thermosets while mitigating their limitations.
A new generation of thermoset material for technical parts
The new generation of thermoset composites developed at CLAYENS addresses many of these challenges. We work closely with material manufacturers, mold makers, and our clients to:
-
Reduce cycle time, aiming for performance comparable to thermoplastics—even for parts with significant thickness.
-
Eliminate deburring operations, which results in significant time savings, reduced material consumption, and a considerable drop in production waste—contributing to more sustainable and responsible manufacturing.
CLAYENS: supporting your projects every step of the way
This new generation of thermoset composites is already being used in client projects, particularly in the electrical sector.
Thanks to our R&D team, CLAYENS is fully committed to helping you select the most suitable materials based on your parts' technical requirements, so we can co-develop a solution that meets the real needs of the market.
*Sprues: The solidified portion of the material through which it is injected into the mold. For thermosets, this portion is typically separated after molding and cannot be reused.